Created in 2007, Kbane designs and implements sustainable solutions for healthier homes that are more energy efficient and more environmentally-friendly. Set up at 5 distinct sites (3 stores and 2 warehouses), Kbane has a current workforce of 83 employees and offers 3 types of services: consulting, installation, and self-serve retailing. The company hires its own installers (i.e. subcontractors are not used). Each of Kbane's trades entails a number of specific risks; safety therefore lies at the heart of the company's concerns.
KBANE - GROUPE ADEO: Safety concerns given top priority
3. Labor relations / working conditions
Workplace health and safety
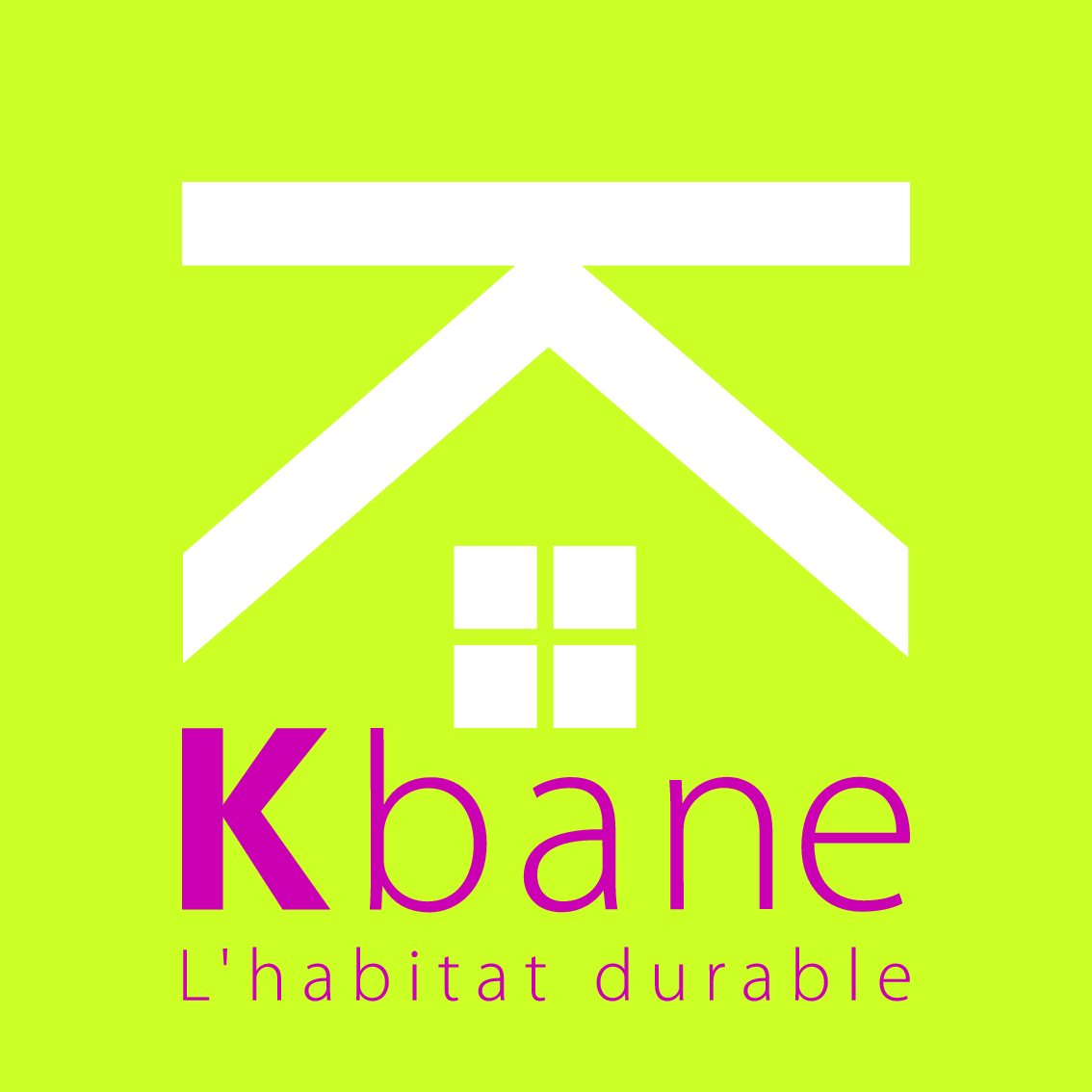
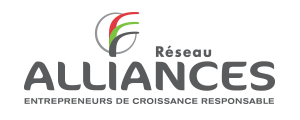
Context
Objectives
- Protecting personnel, clients and neighbors on each job undertaken
- Providing all employees with a common benchmark, a clear and transparent set of rules
- Displaying exemplary conduct and targeting zero accidents.
APPROACH
Each employee is a precious company resource and must be given the opportunity to perform assigned tasks in complete safety, without exposing oneself or others to hazards. It is essential for team members to fully understand the safety rules applicable to their specific workstation.
Kbane pulls out all the stops to ensure the safety of its personnel:
- Training programs and skill refresher courses are regularly held either in-house or else contracted with external organizations (e.g. Securiform)
- A topic consistently raised during working meetings
- Time slots specially allocated to building employee awareness: "The 15-minute safety review", practiced several times a year.
- Each Kbane installer is equipped with the appropriate and adapted safety gear, offering efficiency and modern convenience to perform whatever tasks the particular job requires.
- The more specialized equipment (for working at heights, safety harnesses, supporting props, etc.) is to undergo periodic inspection.
- Every installation team carries in its company vehicle a set of the 8 "Kbane professional safety fact sheets", recalling the safety-related requirements for each aspect of their trade.
- Controls are conducted on a regular basis by the Safety Manager, whose role is intended to be more educational than punitive.
- A display panel, visible to all, serves to illustrate the current safety topic (e.g. insistence on wearing individual protective gear, use of scaffolding), with a meter indicating the number of days since the last accident as well as the year's best result.
Year 2011 safety budget: over €15,000 in training and equipment (individual gear, harnesses).
CONTRIBUTION TO COMPANY PERFORMANCE
- Improved productivity and less absenteeism
Benefits
Every installer on staff is trained in accordance with their trade certification
- Installers are backed by and appreciate the company's commitment to providing them with the resources to perform their missions in complete safety
- Additional advantage in terms of recruitment policy.
- Workforce
- 83
- Turnover
- n.c.
- Country
- France